Design for Additive Manufacturing
Designing "for 3D printing" requires industry-specific expertise. Traditional CAD design is often not sufficient, or requires some useful precautions for the correct finalization of the design.
You need to learn to prevent errors in the printing phase, paying attention to surfaces, angles, overhangs and design details.
An in-depth knowledge of additive manufacturing technologies allows you to reduce time and costs, right from the early stages of design.
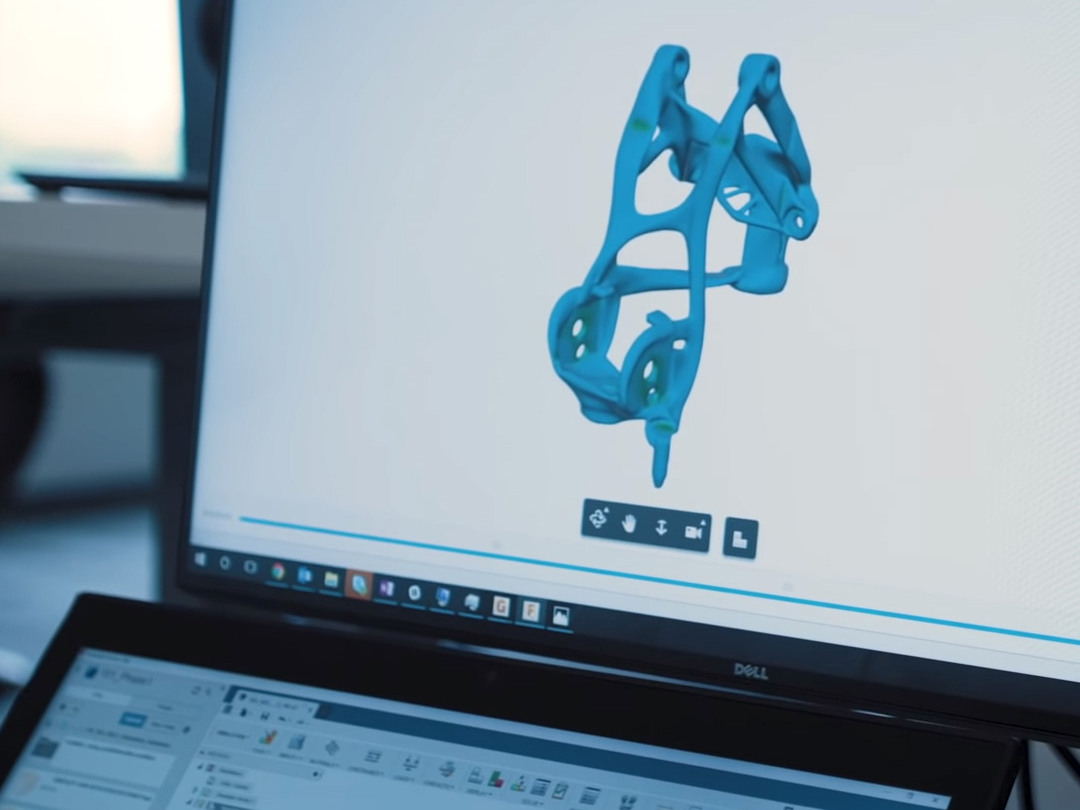
What is Generative Design?
Generative design is a method that is able to simultaneously provide multiple design alternatives starting from fixed boundary conditions (design constraints and loads) and certain input parameters (e.g. cost constraints or production methods). The designer, therefore, can choose the project only among the most valid alternatives developed by the software, drastically reducing product development time.
The advantages of generative design are:
- Offer multiple optimized solutions at the same time
- Simplify your product development workflow
- Achieve unique designs with high performance
Topological Optimization
Topological optimization is the result of a design study with the aim of removing material from a component, while still preserving the required mechanical performance. What you get, therefore, is a design with extremely low weight and resistant. The topological study does not take traditional design approaches into account, going beyond what the human mind can imagine.
This method starts from a Finite Element Analysis (FEM) of the component to be designed, defining all the constraints, loads and boundary conditions to which it is subjected. The topological optimization software carries out a static analysis study of the model, determining stresses and deformations at each point and, in an iterative manner, proceeds to remove material from the less stressed areas and vice versa.
The topological analysis - however - must only be a tool for the designer, who must be able to manage the various production constraints, the design space and the fraction of material that can be removed.
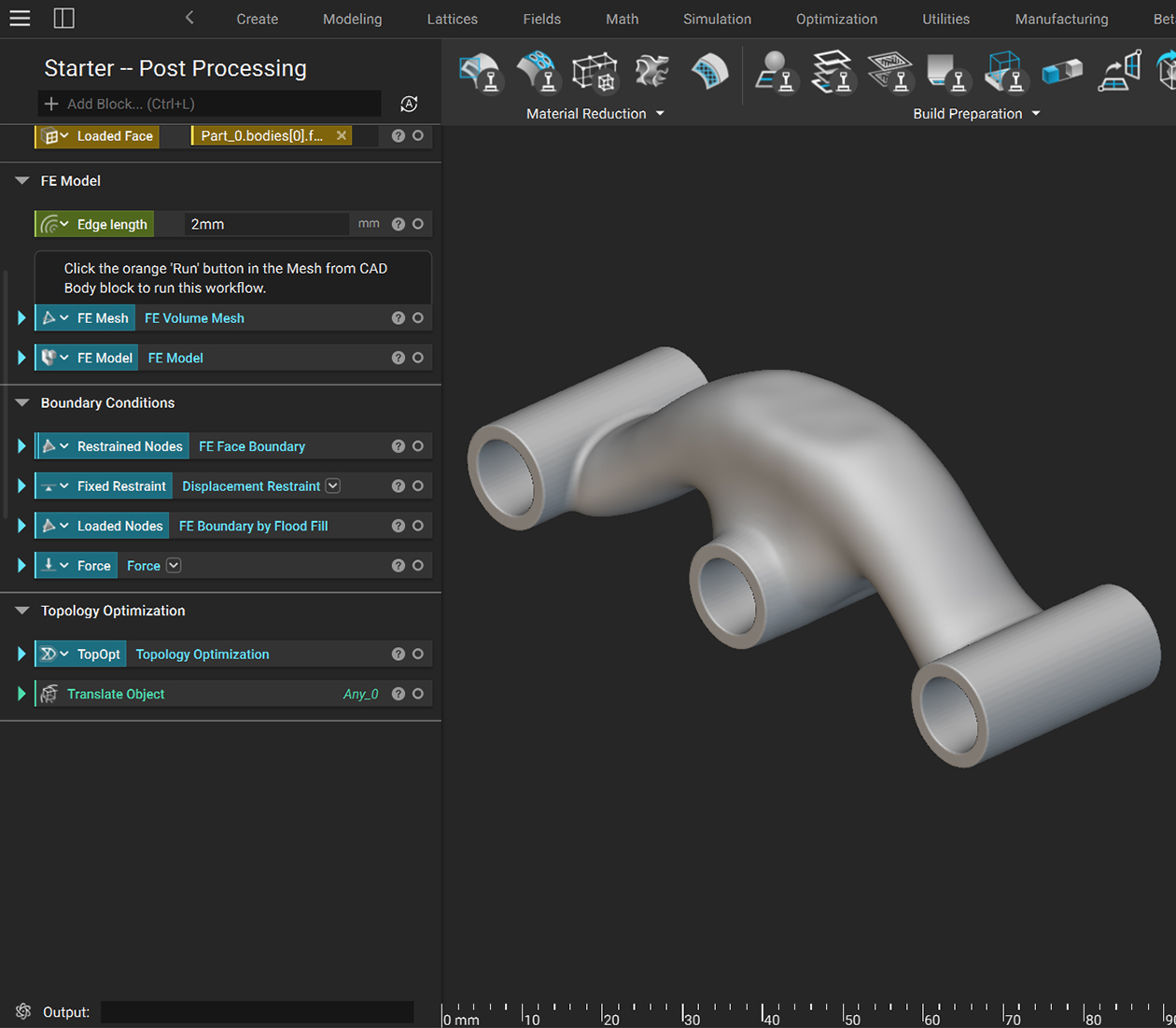
nTop - the most powerful design software
for additive manufacturing
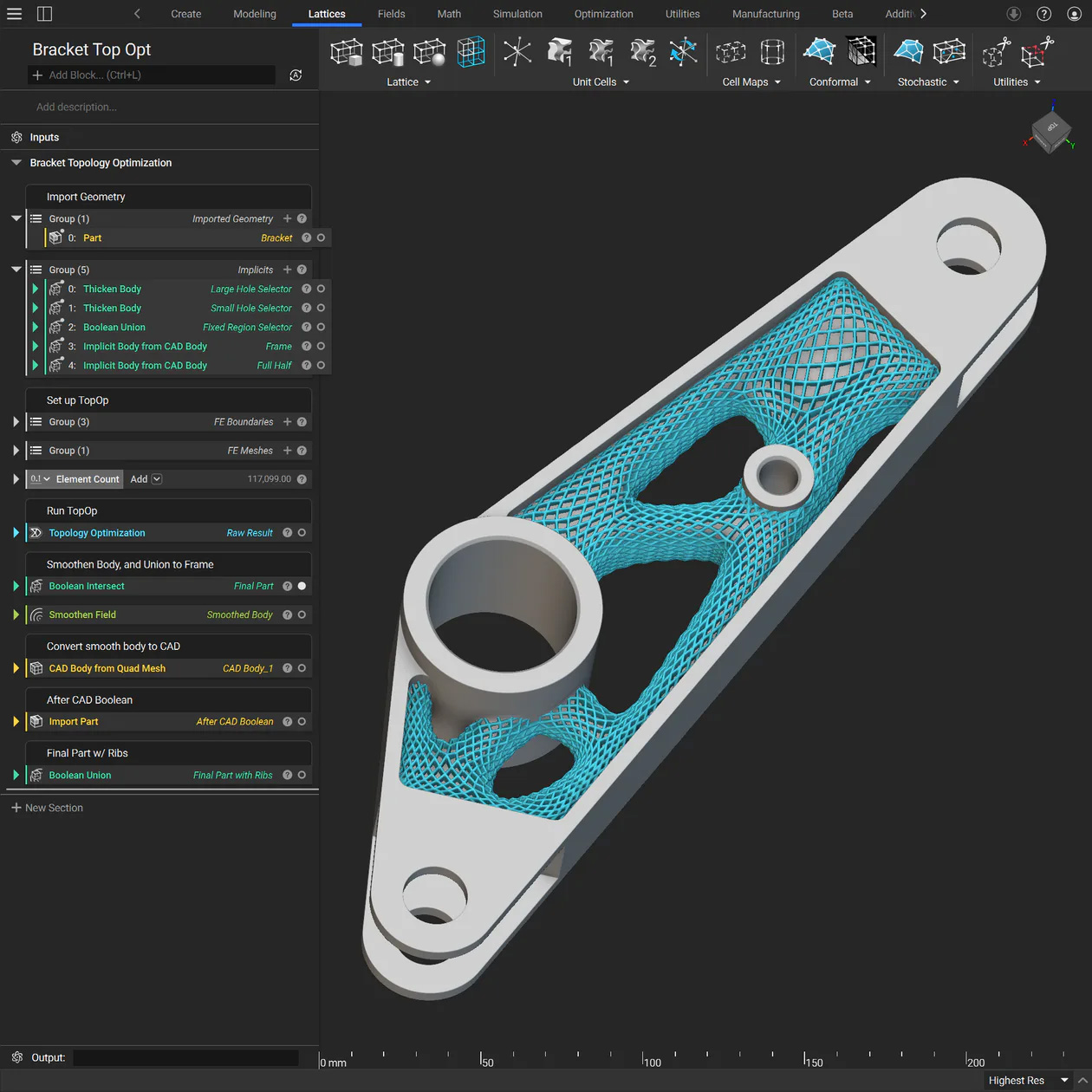
Design
Create unbreakable geometries with the implicit modeling engine. Since every solid body is described as a single mathematical equation, you can adjust and iterate on your designs instantly.
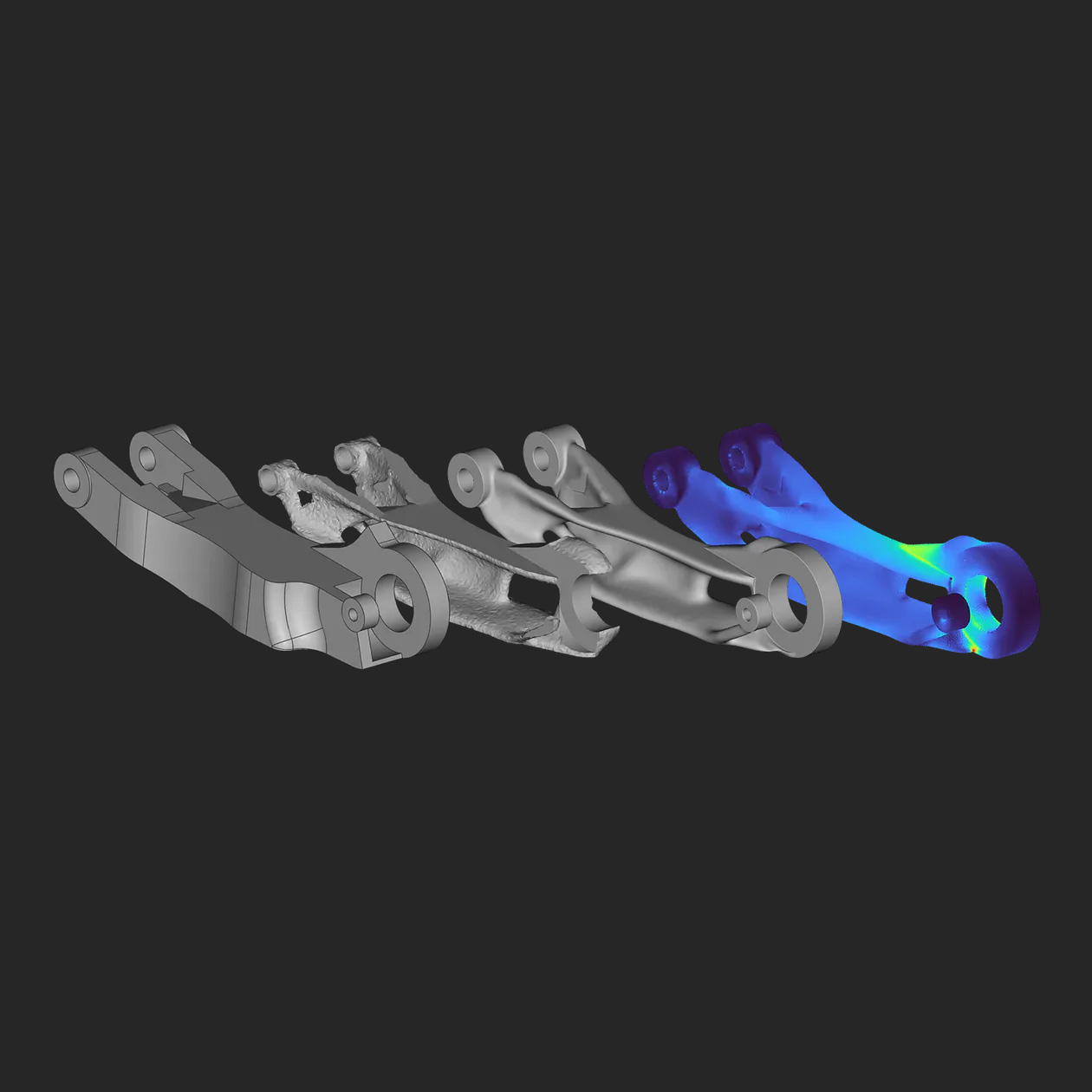
Optimize
Achieve better performance by using Field-Driven Design to optimize based on simulation, test, or analytical data. Take advantage of the best-in-class tools to shorten your design cycles.
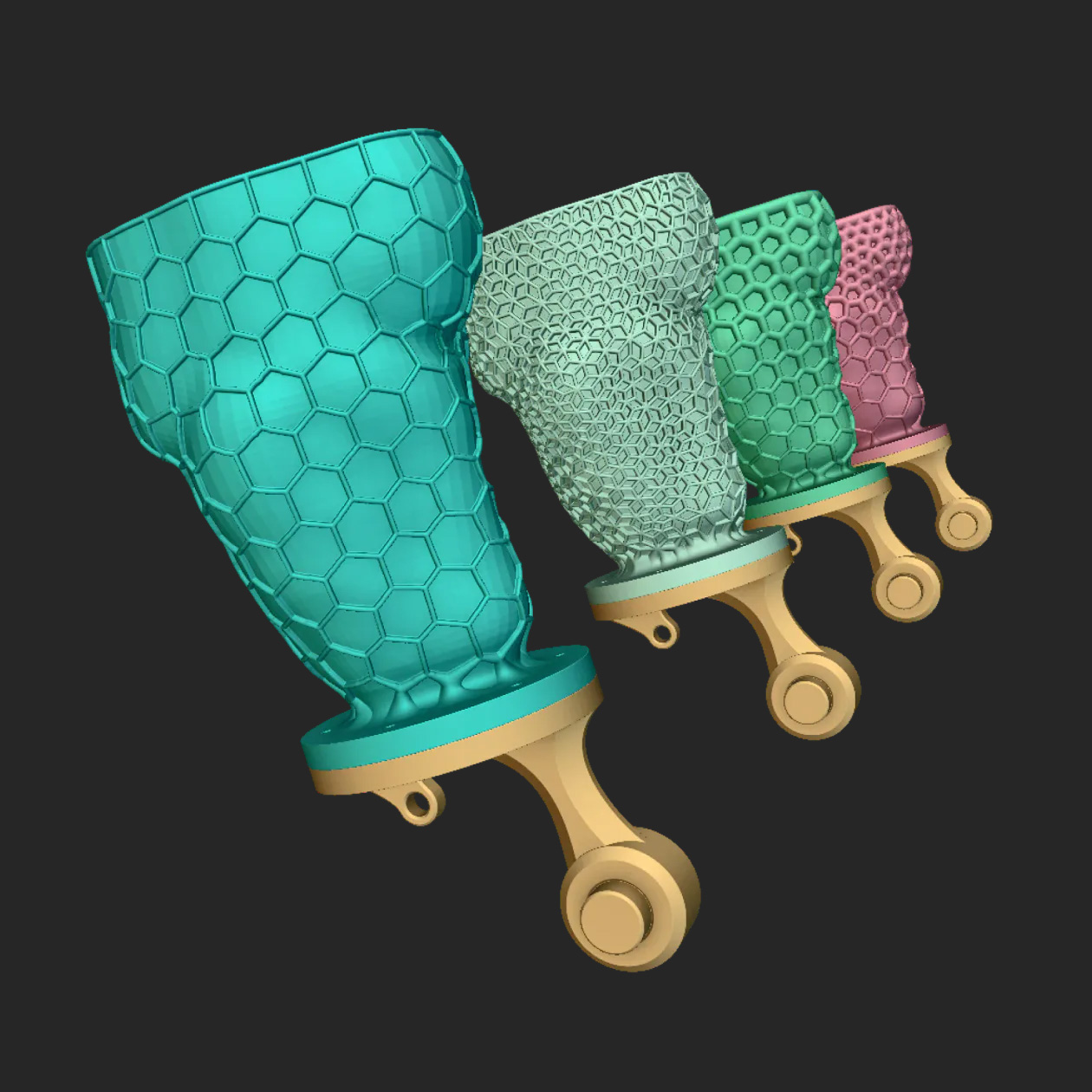
Scale
Create reusable processes to automate repetitive design tasks, batch-process similar parts, and generate multiple design candidates during simulation-driven design.
nTop capabilities
Lightweighting
Additive manufacturing allows the creation of complex geometries that cannot be obtained using conventional subtractive manufacturing technologies. nTop exploits this potential to generate designs with a notable reduction in weight, preserving the mechanical characteristics and structural integrity of the component.
Fillings with lattice structures, parts with variable thickness, ribbing on complex surfaces are just some of the lightening techniques available, allowing the reduction of the masses of a system in order to significantly lower the material cost and improve its performance, efficiency or ergonomics.
Topological Optimization
Topological optimization is the result of an iterative process that is applied to a geometry in order to minimize the necessary material. Through a finite element simulation process (FEM Simulation), the software removes material from the least stressed areas, generating a new design that respects all geometric and technical constraints.
With nTop it is therefore possible to explore various lighter design possibilities, maximizing the mechanical properties of the component.
Texturing and customization
nTop is able to create high quality and customized designs tailored to the customer. Mass customization with Additive Manufacturing is applicable in many fields such as automotive due to the ease of generating logos, textures, reticular structures on the interior and exterior design elements of vehicles; or in the production of consumer goods, creating more ergonomic and comfortable tailor-made products.
FEM simulations
The finite element simulation study (FEM Simulation) allows you to analyze the mechanical and/or thermal behavior of a system under certain load applications and boundary conditions. nTop carries out mechanical studies (static analyzes to determine stresses and deformations of the system, buckling analysis or study of vibration modes) and thermal.
From the results obtained from the simulation it is possible to develop the design that best responds to the behavior of the system, with the advantage of obtaining more efficient, lighter and more compact components.
DfAM
Optimizing the design for Additive Manufacturing requires strong knowledge and experience of the technological process. To these, we add the potential of nTop, allowing you to adapt the geometry for the additive process in a simpler and faster way. In this way the production cycle is faster and more economic.