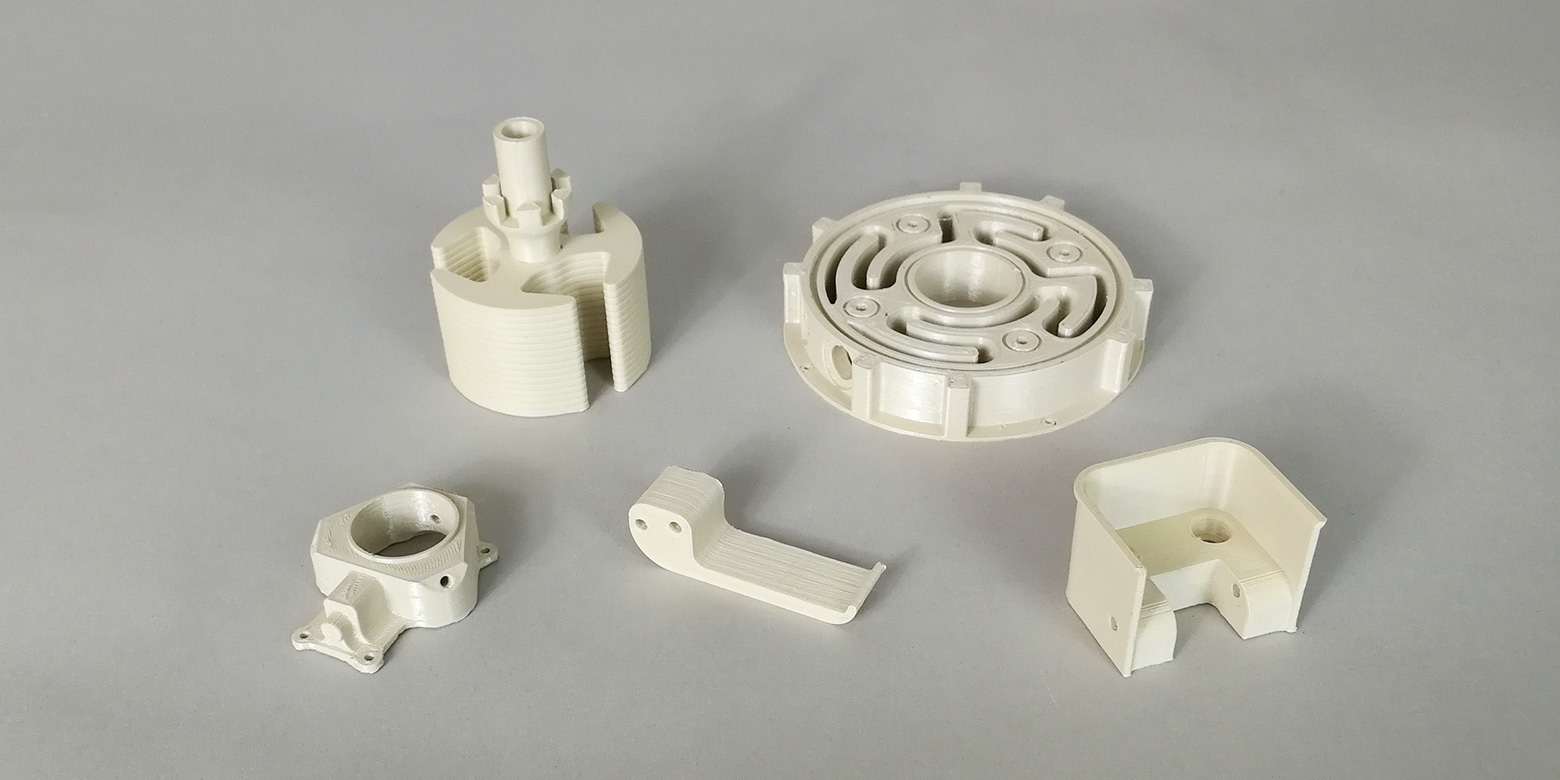
PPS: thermal and dimensional stability, chemical resistance
PPS stands for thermal stability, dimensional stability, chemical resistance and self-extinguishing in case of contact with flames.
"The best compromise between high performance, low cost and ease of printing."
What is PPS?
PPS (Polyparaphenylene sulphide) is a thermoplastic whose molecular structure forms very stable crystalline lattices from a thermal point of view and this allows it to reach a high melting point of about 285°C.
Numerous chemical corrosion tests of PPS have shown that there are no solvents that attack the material at temperatures below 200°C.
The main characteristics of the material are summarized below:
- Thermal stability up to temperatures of 200°C and resistance for short periods of time to temperatures reaching 230°C
- Chemical resistance to a wide range of solvents and organic chemicals even at very high temperatures
- Dimensional stability of simple and complex parts ensuring the dimensional tolerances of easy-to-print materials such as PLA
- UL94 V0 extinguishing rating (less than 10 seconds) without flame retardant additives, this being an intrinsic characteristic of PPS polymer
Applications
PPS is the ideal choice for these industry applications:
- Automotive
- Electronics
- Industrial automation
- Oil&Gas
- Transportation (Railway, Naval)
- Racing/Motorsport
When dealing with components of cars or means of transport subjected to high temperatures, or exposed to oils, fuels or mechanical stress, Fabbrix PPS is the ideal choice.
Typical applications include under-hood components where the current alternative is fiberglass, which is complicated to process and extrude, or for brake systems and electrical/electronic devices which require high heat resistance, high dimensional stability and resistance to corrosion.
PPS Fabbrix PPS is a lighter alternative to metals, resistant to corrosion by salts and all automotive fluids.
Examples of applications in the Automotive sector
• (ETC) Electronic Throttle Control
The Electronic Throttle Control System includes the accelerator pedal, ETC module and throttle body. A multiplicity of these elements can be made with PPS both in the prototype phase and as finished components with the aim of reducing the weight and cost of the metal components.
• Intake manifolds and air and exhaust gas outlet ducts
• Alternator components
Sensors, switches and casing in PPS with the aim of reducing the weight of the components while guaranteeing thermal stability.
• Braking Systems
Sensors for ABS brakes, electric brakes, ESC connecting pistons, valve bodies
• Fuel Rails
They are pipes that carry fuel to the injectors in an internal combustion engine. PPS resists the passage of combustibles.
• Covers, caps and impellers of the fuel pump or the oil pump
Examples of applications in the Industrial and Automation sector
• Turbocharger components
Carter, Turbine, Conveyor can be made in PPS, still guaranteeing dimensional stability even at high temperatures.
• Centrifugal Pump Components
• Diverters and ball valves
PPS guarantees thermal stability in contact with hot water.
Examples of applications in the Electrical/Electronics sector
• Terminals and connectors
These elements require UL94 V0 certification which the PPS Fabbrix is equipped with.
• Cooling unit for electric motors
The fluids used as refrigerants attack normal plastics but not PPS.
• Rotors or other components of electric motors
• Consumer Electronics components
As a good standard for consumer electronics components, it is essential that the UL94 V0 certification is not due to additives but is an intrinsic property of the material.
Therefore, if we consider thicknesses >3mm (according to regulations), PPS does not trigger the so-called flashback, while the other polymers tend to facilitate combustion. Furthermore, the PPS does not release incandescent drops, thus avoiding the start of a fire in other points.
Dimensional and thermal stability, chemical resistance and V0 certification according to the UL94 standard make PPS the material of the present and the future for functional prototyping and the production of final parts.