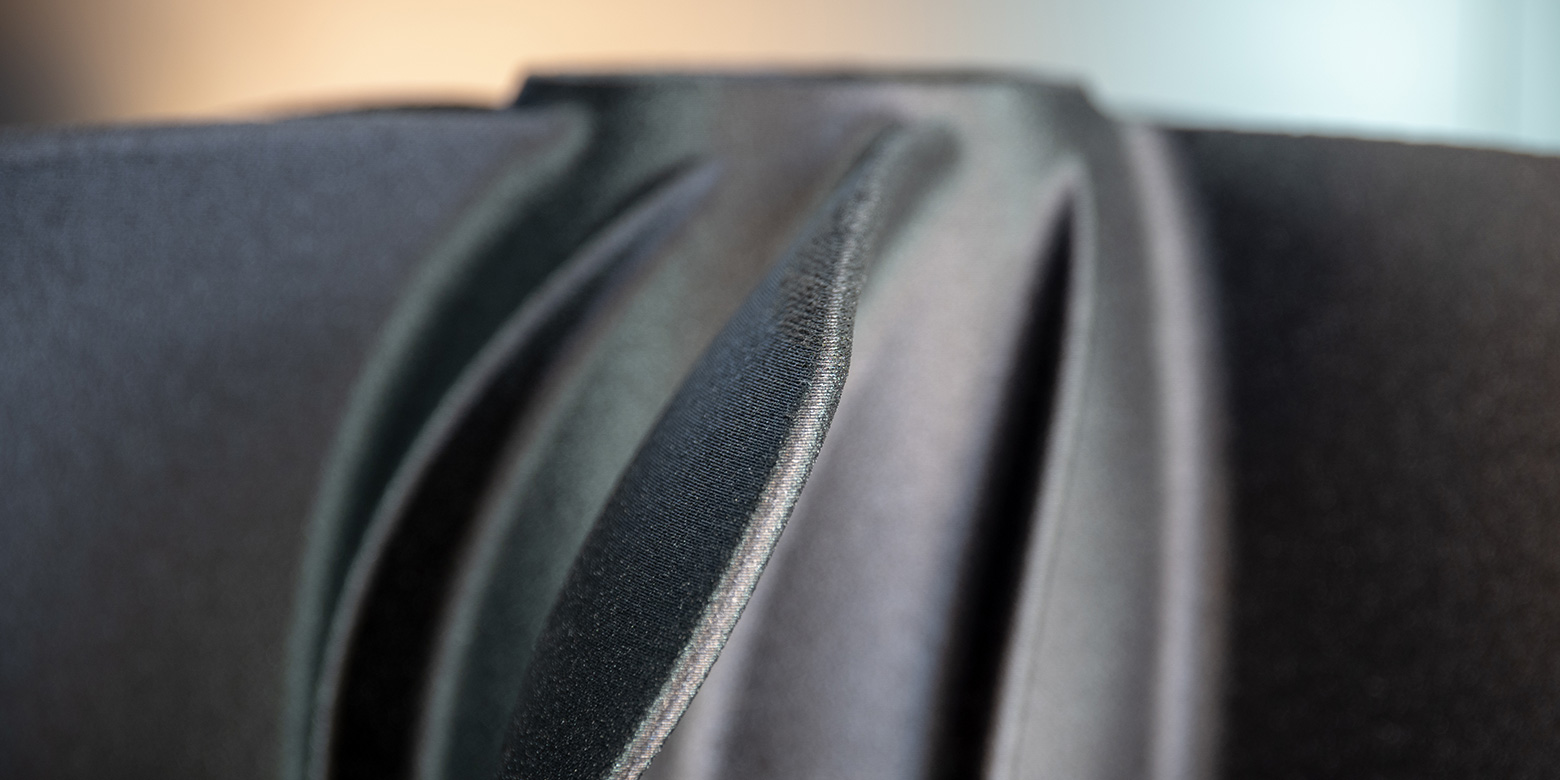
Composite materials for Additive Manufacturing
A composite material is a combination of two or more simple materials, in order to take advantage of the qualities of the constituents and to improve their mechanical characteristics.
Fibers and matrix are combined: the MATRIX acts as a binder and as a support (in compressive stress) and the FIBERS act as a reinforcement (in tensile stress).
Numerous advantages are found and the following properties are improved:
- Mechanical strength;
- Stiffness;
- Weight (less than 25%);
- Corrosion resistance;
- Resistance to dynamic stresses (shocks and fatigue);
- Internal damping of the material;
- Soundproofing;
- Resistance to chemical aggression and unassailable by molds and microorganisms;
- Crash energy absorption capacity;
- Stress distribution on a very high number of fibres;
- Possibility of obtaining materials with thermal and electrical conductivity characteristics suited to the needs;
Despite these advantages, however, composites also have disadvantages which can be summarized as follows:
- High cost compared to light metal alloys (about 3 times);
- Difficulty in reusing and disposing of materials;
- Repair of artifacts often completely ineffective (irreversibility of damage);
- Difficulty in checking and analyzing the integrity of materials;
- Lower strength and hardness of the matrix compared to the fibers;
- Transverse properties sometimes much lower than those in the direction of the fibers (anisotropic material);
- Possible aging of the matrix material.
Fibers
Carbon fiber: composite materials manufactured using carbon fibers as reinforcement of polymeric resin matrices such as epoxies, are characterized by having a good combination of light weight, high mechanical strength and high stiffness (modulus of elasticity).
These properties make the use of composite polymeric materials with carbon fibers for aerospace applications particularly interesting; unfortunately, the relatively high cost compared to glass fibers makes the latter more widely used thanks also to their versatility. They are produced by PYROLYSIS (breaking of macromolecules and heating), CARBONIZATION (allows to obtain elementary carbon; T=1000±1500°C) and GRAPHITIZATION (allows to obtain carbon in crystals to increase resistance and elastic modulus; T= 1800°C) of RAION, POLYACRYLONITRILE (PAN) or other synthetics.
Commercially, the fibers produced by RAION are processed in the form of a continuous yarn, which consists of 2 threads twisted together, each consisting of 720 filaments. The nominal diameter of the yarn is about 5 μm. PAN-based fibers are instead supplied in the form of an untwisted rope of approximately 10,000 filaments. Light weight, high stiffness, excellent mechanical characteristics.
Glass fiber (type E and type S): they have lower tensile strength and modulus of elasticity than carbon and aramid fibers but higher density and elongation capacity.
Glass is characterized by its own behavior which is not of the solid type: over time there is a sliding of the fibres.
Matrices
Thermoplastic resins: polymeric material that softens if brought to temperatures close to the melting point, and hardens if brought to room temperature.
- Polyetheretherketone (PEEK)
- Polyethereketone (PEK)
- Polyetherimide (PEI)
- Polypropylene (PP)
- Polyamide (PA)
Tensile strength
The stress-strain diagram contains the constitutive bond of the fiber and the matrix, but also the ability of the fibers to resist much higher stresses than those applied to the matrix alone, and the ability to deform of the matrix. During a tensile test, the fibers and matrix are initially in the elastic range, after which the fibers continue to deform but the matrix will be in the plastic range. So in summary, what can happen is:
- Elastic deformation F+M;
- The fibers deform elastically but the matrix is in plastic conditions (even if it happens that the F break before M plasticizes);
- F+M plastically deformed;
- The fibers fracture, the composite also fractures.
Compressive strength
The fibers are constipated by the matrix, i.e. we will have the effect of the matrix which hinders the movements of the fibers. In this case it is difficult to talk about critical load. What we can do is define two cases: subjected to compressive loading, the lamina can deform according to an extension mode or according to a shear mode. In the first method we have that the deformation of the individual fibers, due to the percentage of the fibers and the load I am applying or due to discontinuity of the matrix, the deformation are in phase opposition, therefore, tensile and compressive stresses are generated in the matrix . In shear mode the fibers deform "in phase" and shear stresses are generated. In this case we have the buckling phenomenon. as the % of the fibers increases, the resistance to buckling grows more in the extension than in the shear mode.
3D Printing
3D printing presents itself as a solution to multiple problems, both of an engineering and environmental nature. Carbon and glass fiber reinforced composites are widely used in 3D printing technologies.
For example, the following figure shows components similar to cable glands, supports for sensors, made of Fabbrix® Nylon Carbon
The material under examination has good resistance to heat and breakage. Nylon gives toughness and resistance, while carbon ensures lightness and printability.
Printed parts are durable and textured to the touch, with a slightly metallic effect. The material needs to be dried in an oven to eliminate humidity, and this takes place at 75°C for about 5-6 hours.
Printing took place under the following conditions:
- Extrusion Temp: 260 °C
- Printing Speed: 40 mm/s
- Plate: 75°C
The components made are mainly used in applications for the automotive sector, where the continuous demand for materials with high mechanical performance places Nylon Carbon at the forefront of the most processed composite materials with 3D printing.
Contact us for more information
Watch the Crea3D webinar: "Composite materials: 3D printing beyond prototyping" [IT]