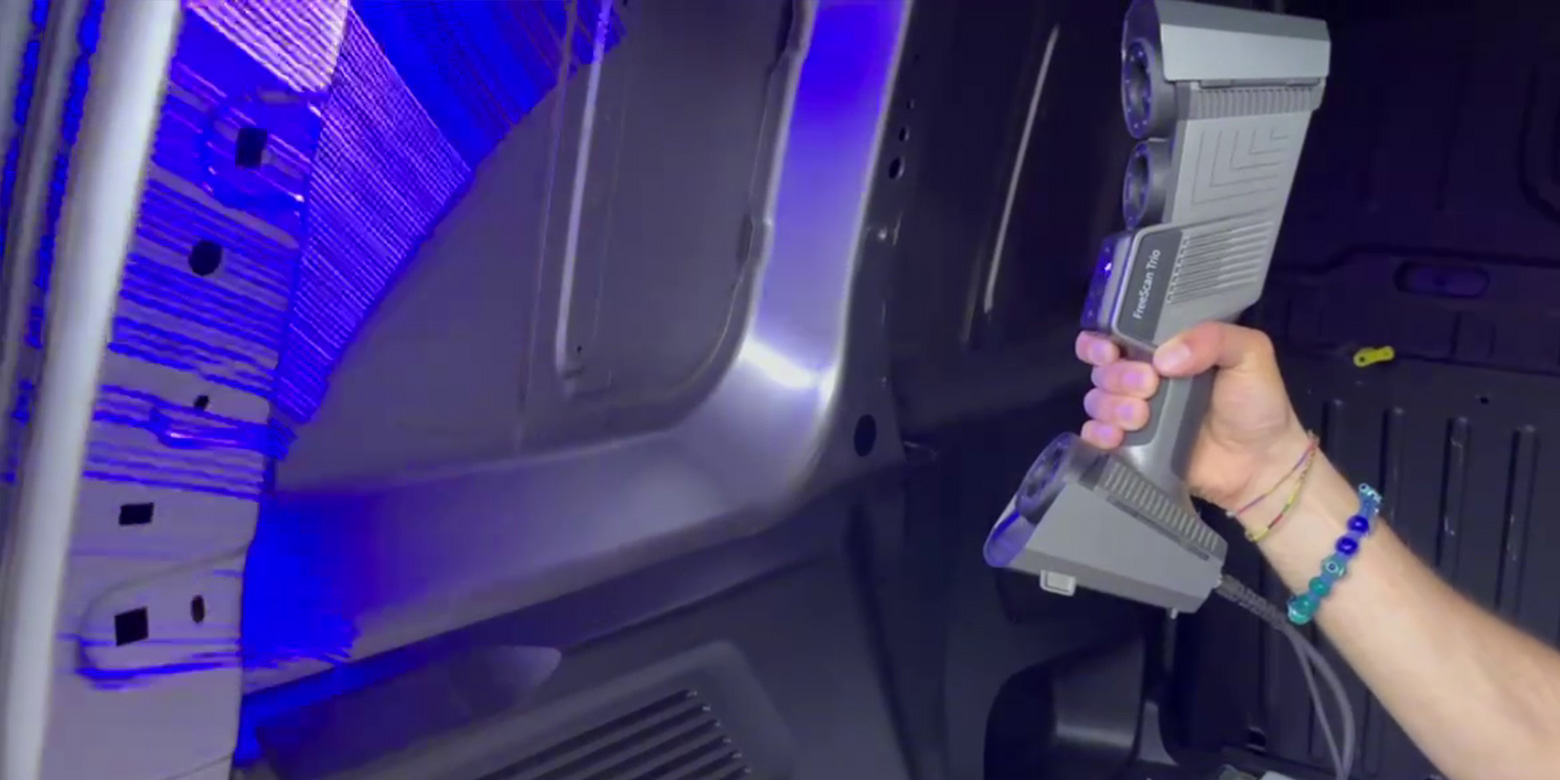
3D scanning for special vehicles setup
Being able to scan large components has numerous applications in the automotive sector, for example for the setup of special vehicles.
In this case, 3D scanning allows you to precisely detect the dimensions and internal geometries of the compartment of a basic vehicle. This information is essential for designing and adapting bespoke setups, such as structures for the transport of specific equipment or customized configurations for particular operational needs.
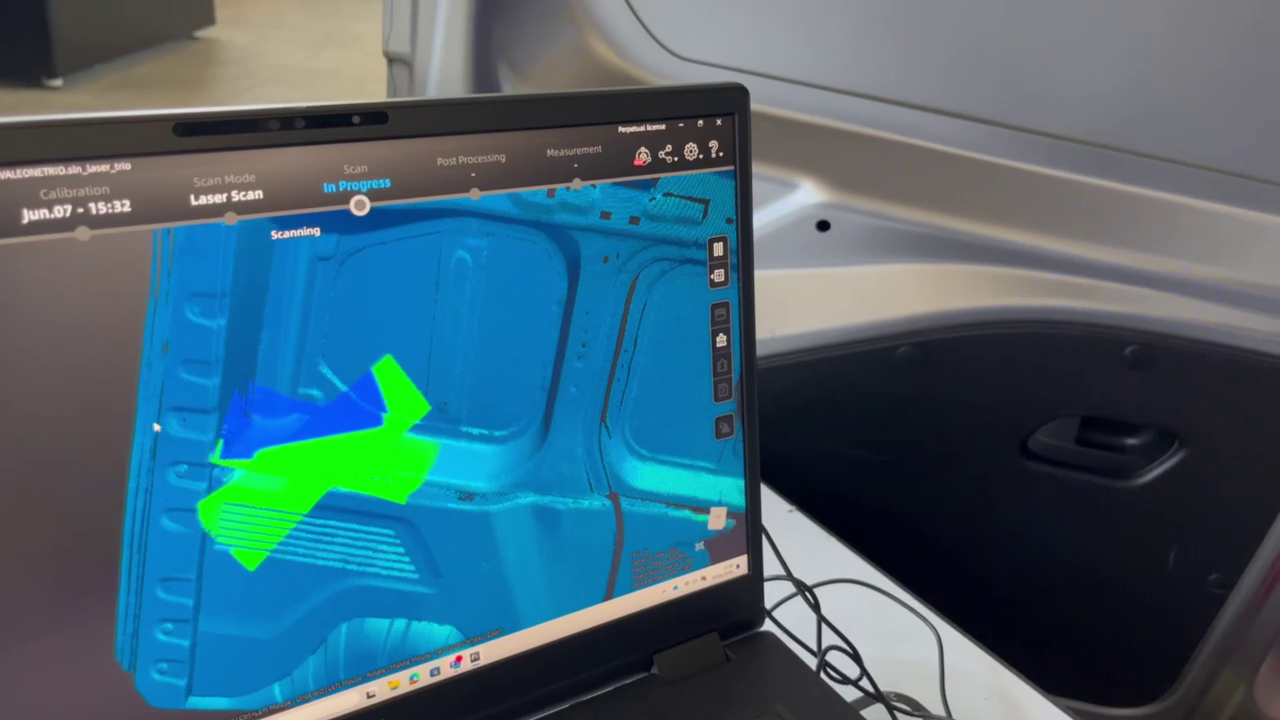
The benefits of in-house 3D scanning
To take measurements of the compartment or trunk of a vehicle, engineers were previously forced to take multiple measurements and with multiple instruments. Time-consuming, laborious and error-prone activity.
Furthermore, one of the most common critical issues in production departments is the inability to move the components to be scanned. The solution is to have a manual and ergonomic scanner to acquire the entire model on site and process the results in real time on a computer, reducing the time needed to collect and document all the characteristics of the compartment.
Freescan Trio for large format scans
To scan the entire compartment of the vehicle, in our example, it was necessary to use the Freescan Trio, one of the 3D scanners from Shining 3D's FreeScan range.
One of the main advantages of this scanner is the “Marker Free” mode, which allows -thanks to the use of 98 laser lines- to scan large format components without the application of reference markers, an operation that would slow down the workflow if the surface to be scanned is very large.
Despite the Trio's ability to acquire large amounts of data quickly (up to 3,010,000 points/s with High Speed mode), its accuracy remains high (0.02mm), as it offers the possibility of using photogrammetry through the use of photogrammetric bars.
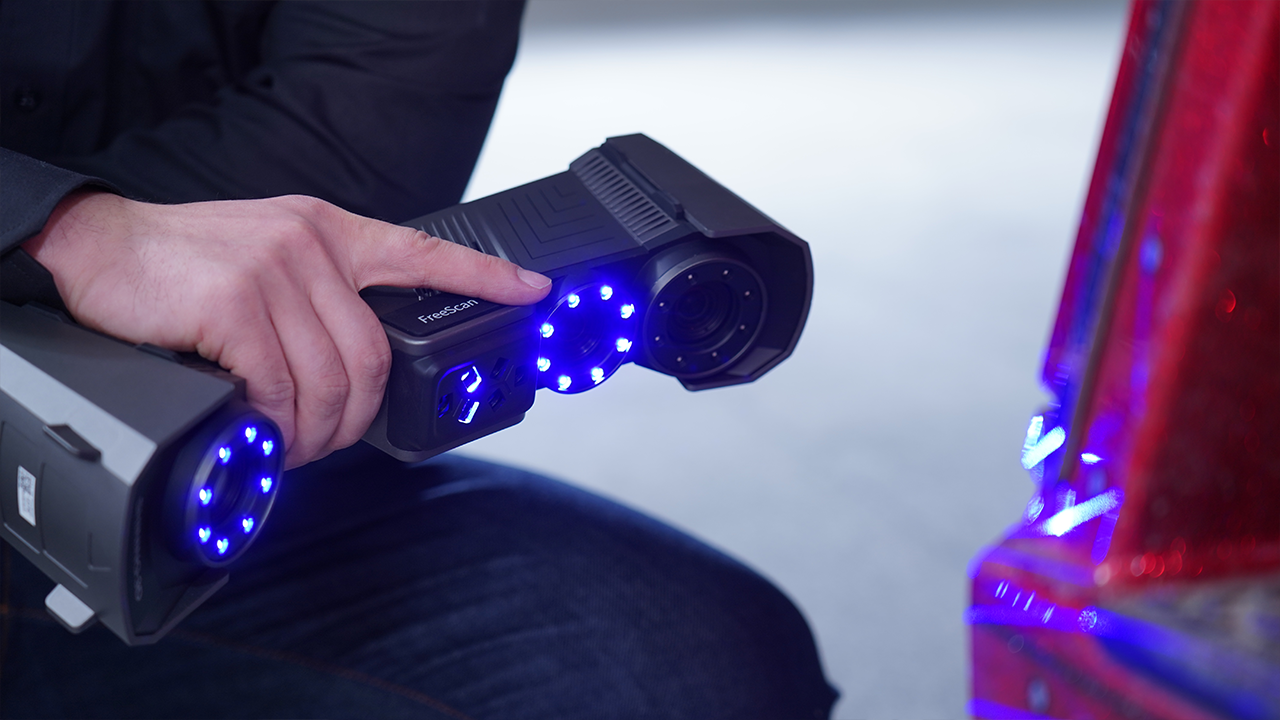
This 3D scanner made it possible to acquire all the different types of paneling in the vehicle compartment, from reflective metal ones to dark plastic ones, which are usually difficult to detect with a structured light 3D scanner, without the use of opaque sprays.
To simplify the workflow and better manage the data acquired on the PC, it is convenient to make multiple scans and then perform an alignment between them, thanks to the automatic and intuitive options of the 3D scanner software.
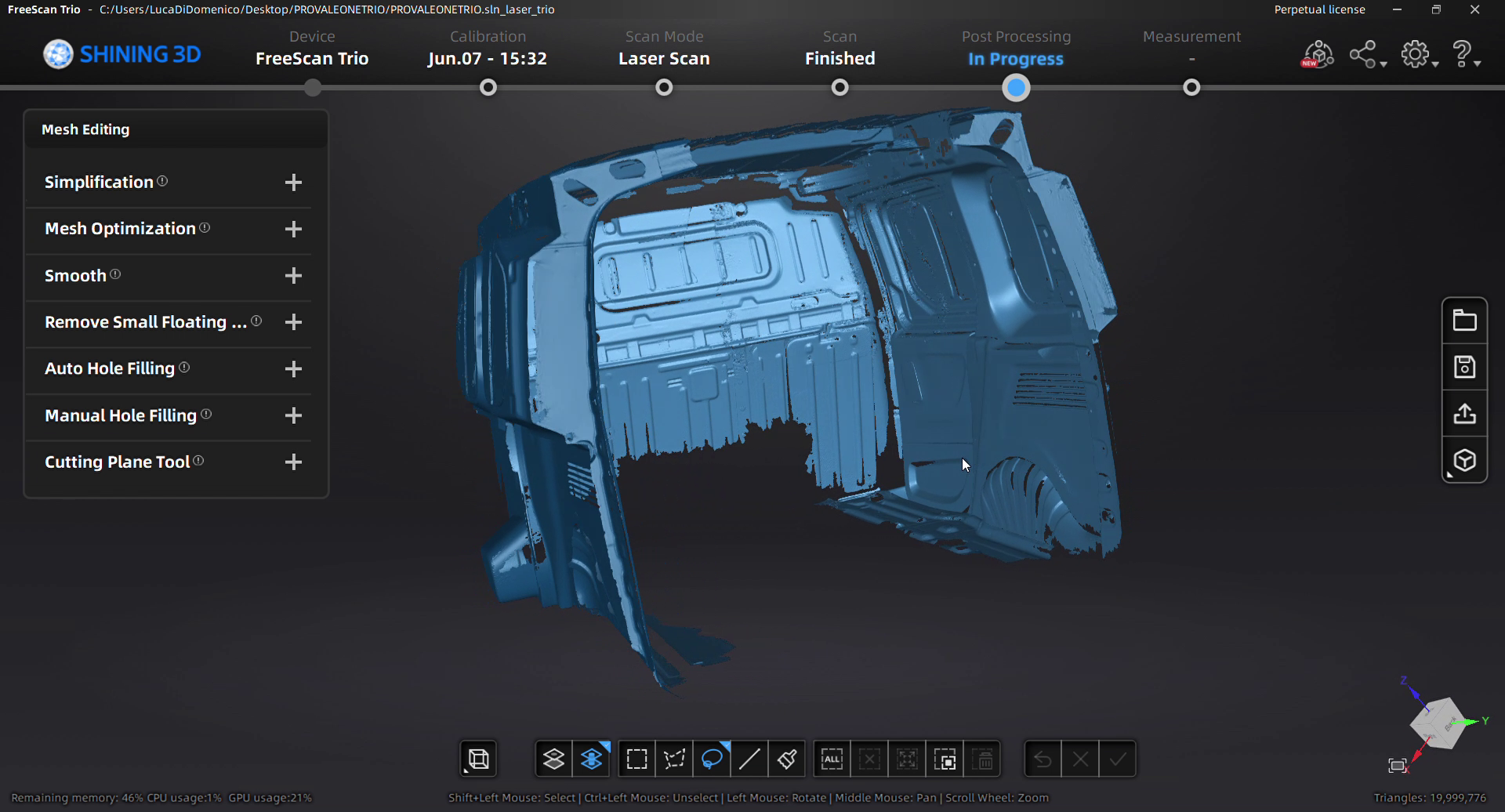
After the 3D scanning process, a mesh is generated, which can subsequently be edited in Reverse Engineering software, such as Geomagic Design X, and used as a reference for designing customized structures, for example creating fastening elements, box-like bodies or beams.
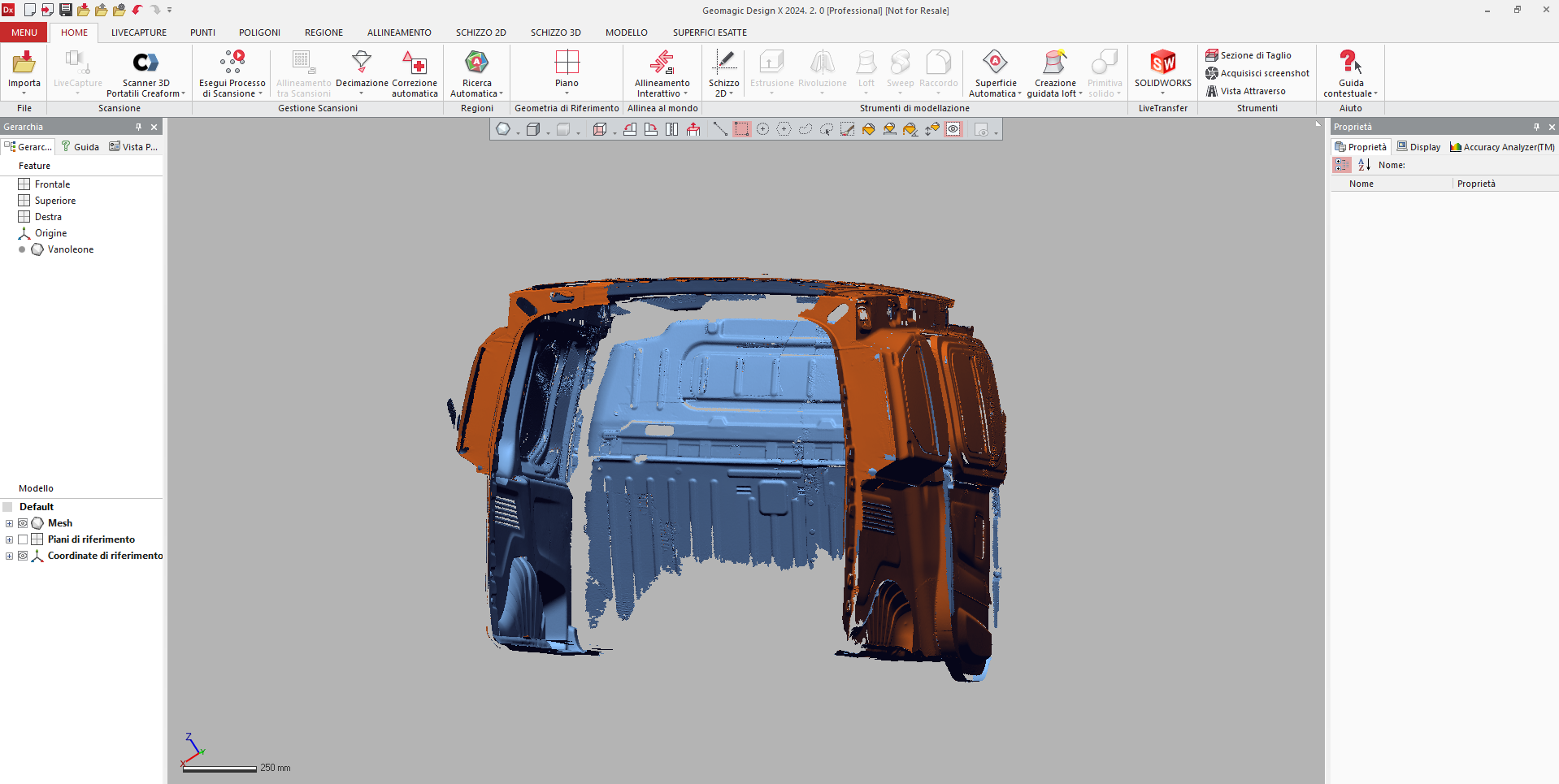
Conclusions
All this means reduction in design and production times and costs to create customized solutions and greater flexibility in managing any design changes.