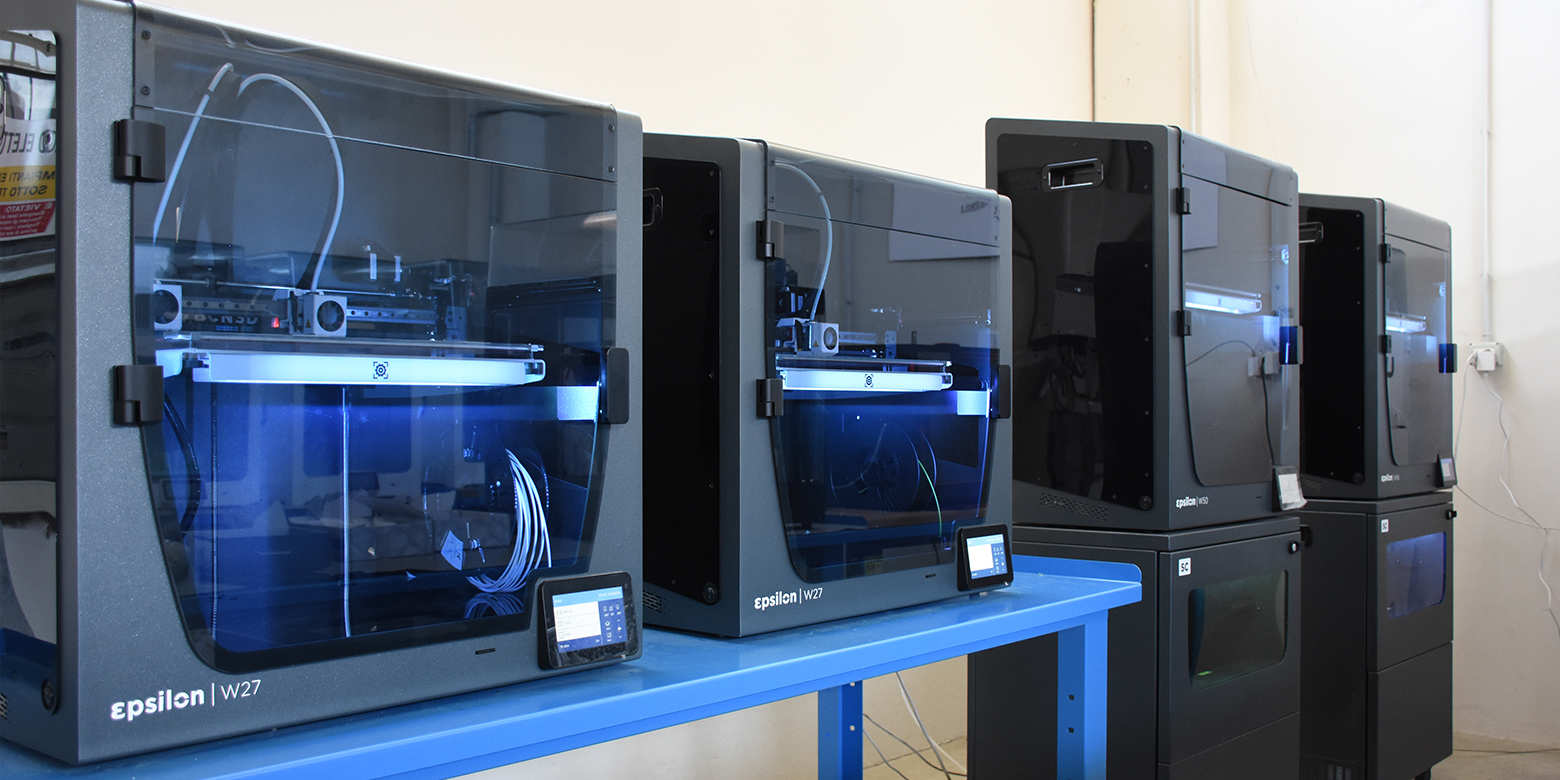
BCN3D Print Farm: the benefits of the IDEX system
In modern companies, the concept of a print farm refers to an automated solution for additive manufacturing, which leverages a fleet of interconnected 3D printers to produce components efficiently and at scale.
The print farm is basically a digital factory, where 3D printers are connected to a centralized network and managed by control software. In general, it allows for continuous and automated production, as 3D printers can be programmed to start printing parts sequentially or in parallel, depending on the needs.
This means that it is possible to achieve increased productivity, reduce waiting times and improve the overall efficiency of the production process. Advanced control software monitors the status of 3D printers, manages the job queue and automatically distributes print files to available printers. In addition, the software can carry out a continuous quality control, verifying the conformity of the produced components and detecting any defects or errors. The print farm also allows you to optimize the use of resources.
For example, if a 3D printer goes down due to a breakdown or need for maintenance, the control software can automatically divert the job to other working printers, avoiding interruptions in production. In addition, the software can also optimize the arrangement of components on the printer's print plate, in order to maximize efficiency and reduce material waste.
Benefits of using a print farm
- Increase in production capacity: the print farm allows for continuous and uninterrupted production, reducing waiting times and increasing overall production capacity.
- Cost reduction: Print farm automation and optimization can reduce labor and material costs, improve overall efficiency and reduce waste.
- Flexibility and customization: the print farm allows you to easily manage the production of customized components or in small quantities, adapting to specific customer needs.
- Quality control: thanks to the advanced control software, it is possible to constantly monitor the quality of the components produced and detect any defects or errors in real time.
- Agility in production: the print farm allows you to respond quickly to market demands, reducing the development and production times of components.
A print farm of BCN3D 3D printers with IDEX technology
And if you have a print farm of 3D printers that use IDEX technology?
BCN3D has developed the IDEX technology, a Independent Double Extrusion system different from the classic print head, as it is made up of two independent extruders that can either compete in the creation of the same print, or create two objects simultaneously. Compared to a traditional system, there can be no molten material from one nozzle interfering with parts printed by the other operating nozzle, as the inactive printhead remains stationary and parked to one side of the build plate. The IDEX system also makes it possible to have very light indirect type extruders, therefore with a motor distant from the print head, and this lightness is transformed into very low inertias of the print head and therefore repeatability in positioning and perhaps even printing speed that with extruders direct cannot be reached.
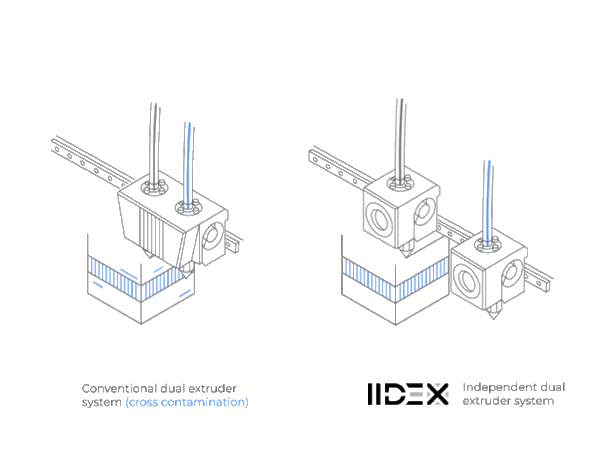
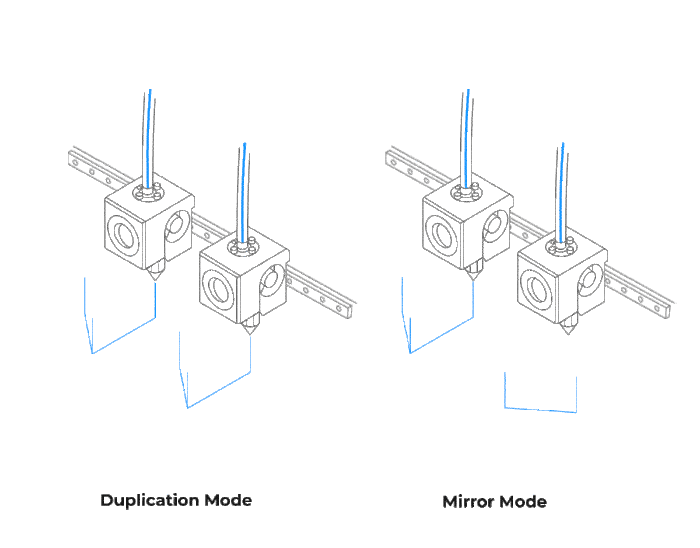
Doubling productivity
By using a print farm of BCN3D 3D printers with IDEX technology you are able to increase productivity, doubling the production capacity compared to traditional printers.
Thanks to its duplication and mirror printing modes for the production of low volume batches, IDEX technology offers many advantages:
- Halves the cost of machinery: with the same number of 3D printers, the end customer can get twice as many printed parts as with other dual extrusion machines without IDEX.
- Cut maintenance costs and downtime in half: Standard maintenance is required to keep a 3D printer in top condition. Since there are no additional actions or maintenance costs compared to other 3D printers when you invest time in maintaining a BCN3D printer, you effectively get double the output.
- Cut labor cost in half: Designing and setting up for printing on BCN3D printers takes the same amount of time as any other machine on the market. However, investing in a BCN3D printer this time produces twice the parts.
- Same space, double productivity: since BCN3D printers double production, every square meter used to house a printer produces twice as much.
Our print farm currently consists of 4 3D printers, all from the BCN3D Epsilon range, two W27 and two W50 SC. Processed materials: PLA, PLA PRO1, Tough PLA, ABS.
BCN3D |
BCN3D |
BCN3D |
BCN3D |
|
Power (KW) |
0,6 |
0,6 |
0,6 |
0,6 |
Hours of use in a day (h) |
8 |
8 |
8 |
24 |
Number of parts printed per day, on average |
16 (IDEX) |
16 (IDEX) |
1 (single extruder) |
1 (single extruder) |
Number of parts printed per month (Jan-Jun) |
764 |
240 |
20 |
22 |
Energy consumed per day (KWh) |
4,8 |
4,8 |
4,8 |
14,4 |
Energy consumed per month (20 days)(KWh) |
96 |
96 |
96 |
288 |
Energy consumed per year (11 months)(KWh) |
1056 |
1056 |
1056 |
3168 |
Market price of kWh (€/KWh) |
0,068 |
0,068 |
0,068 |
0,068 |
Energy cost per day (€) |
0,3264 |
0,3264 |
0,3264 |
0,9792 |
Energy cost per month (€) |
6,528 |
6,528 |
6,528 |
19,584 |
Energy cost per year (€) |
71,808 |
71,808 |
71,808 |
215,424 |
Going into detail, we have taken this component as an example which requires a production of at least 1000 pieces.
By slicing on BCN3D's Stratos software, you can see how in a working day you can produce about 16 pieces.
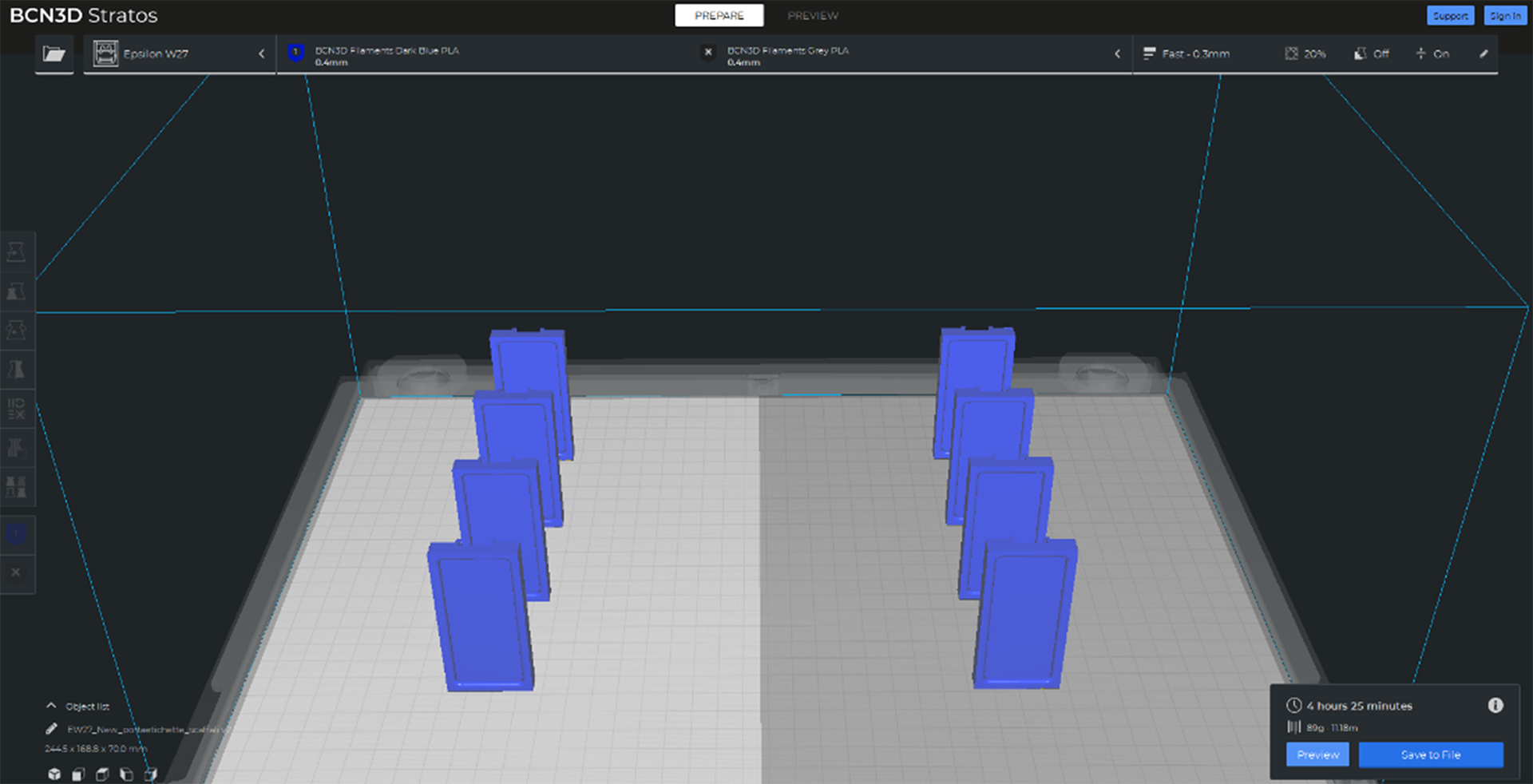
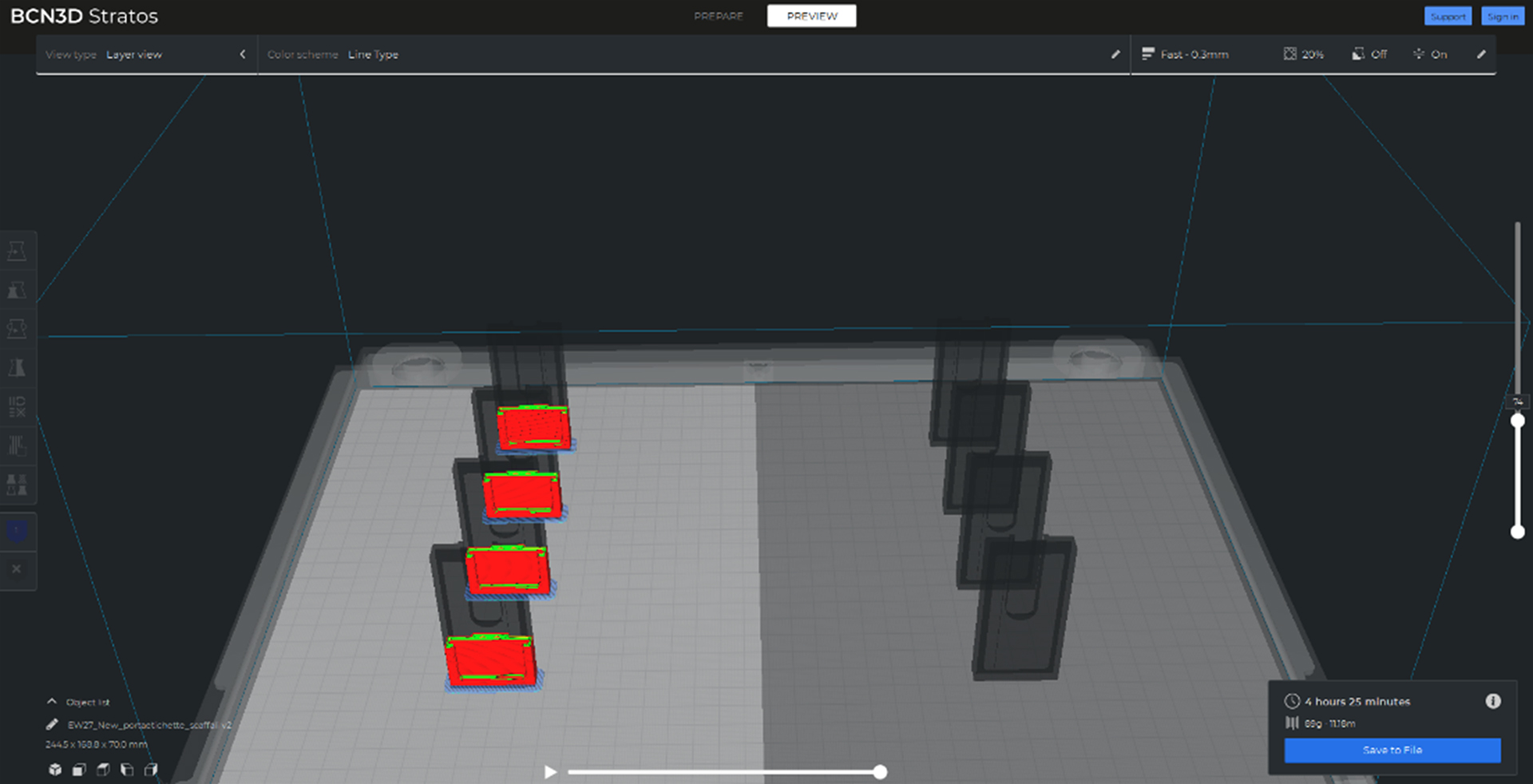
Dual extruder |
BCN3D |
|
Power (KW) |
0,6 |
0,6 |
Hours of use in a day (h) |
8 |
8 |
Number of parts printed per day, on average |
8 |
16 (IDEX) |
Number of parts printed per month (Jan-Jun) |
676 |
852 |
Energy consumed per day (KWh) |
4,8 |
4,8 |
Energy consumed per month (20 days)(KWh) |
96 |
96 |
Energy consumed per year (11 months)(KWh) |
1056 |
1056 |
Market price of kWh (€/KWh) |
0,068 |
0,068 |
Energy cost per day (€) |
0,3264 |
0,3264 |
Energy cost per month (€) |
6,528 |
6,528 |
Energy cost per year (€) |
71,808 |
71,808 |
In conclusion, a comparison between a printer with IDEX technology and a standard 3D printer with dual extrusion shows how, with the same consumption and energy costs, a BCN3D printer produces twice as many components in one working day, increasing production by 26%. The data shown in the previous table illustrates this comparison by taking into consideration the same component produced with two different machines.
For this reason, for high mass production, the IDEX system is convenient, in accordance with what was previously described.