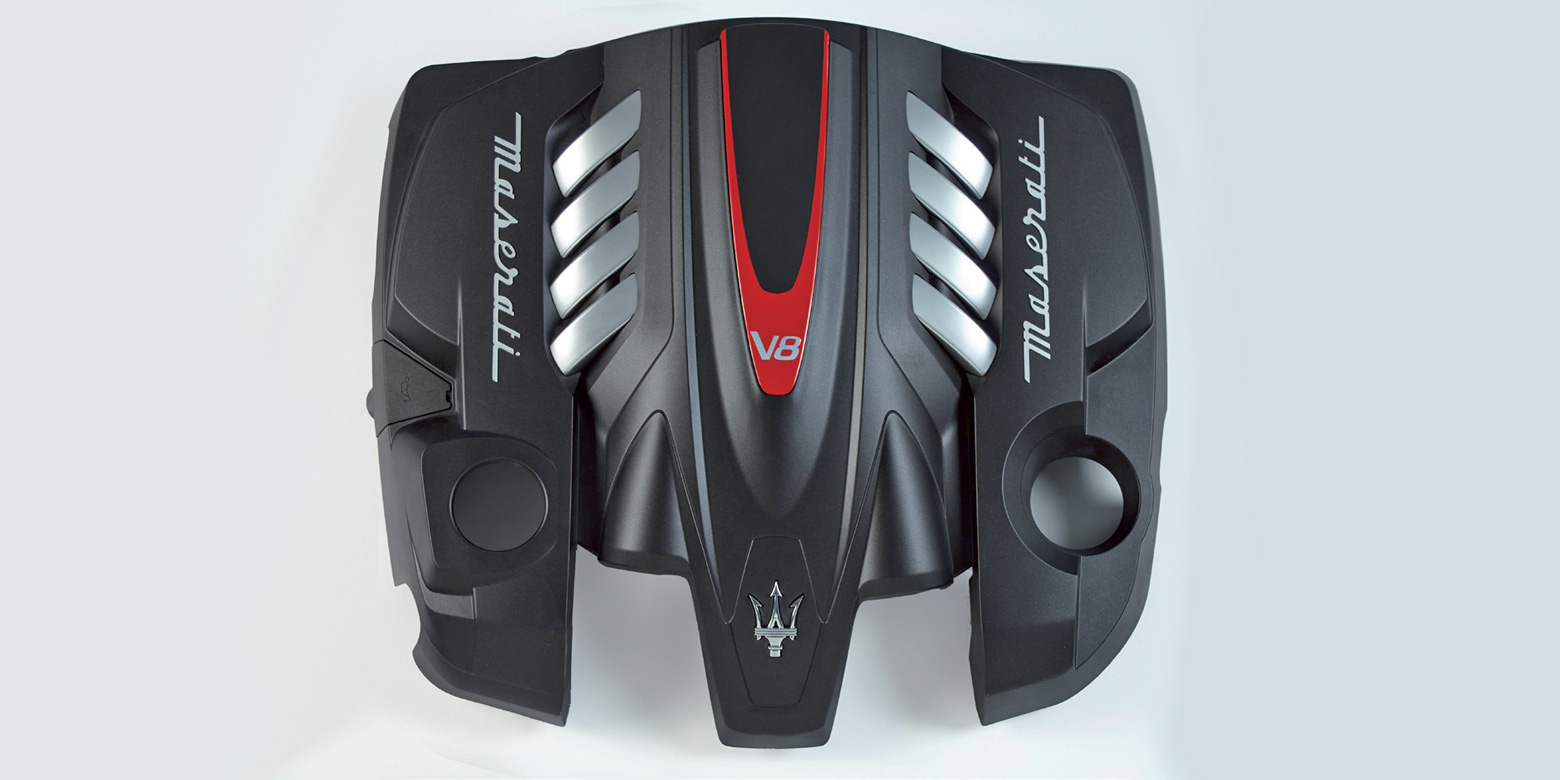
Replacing aluminum with polyamides is now possible!
Glass fibers are the most commonly used reinforcement in filled polymers.
Glass filled polyamides (nylons) successfully replace metals in engine and underhood components.
In cars with combustion engines, polyamides are used in various formulation variants, often filled with glass fiber present up to 60%.
Even the electrical sector of e-mobility is a privileged application area for polyamides. Just think of flame retardant materials.
Which polyamide to choose?
The automotive market considers, where possible, the use of PA6, which is configured as a possible alternative to metals, due to its interesting mechanical characteristics, easy printability and competitive costs.
The performance differences in properties such as modulus and tensile strength of 'dry as molded', dry and room temperature polymers of PA66 and PA6 are relatively small, however they vary significantly, in favor of PA66, evaluating the product that has absorbed the humidity of the environment, generally in relative values of 50-60% and more.
Design the component according to the polymer used.
First of all, it is necessary to take into account that it may be necessary to increase the percentage of glass fiber filler in the PA6 to compensate for the lower breaking strength due both to the absorption of humidity and to the presence of high temperatures of use.
The following table shows the mechanical properties of PA66 and PA6 filled with glass fibers. The tests are carried out at a temperature of 23°C.
Besides the mechanical characteristics, there are also the thermal ones to be taken into consideration. Below are the stress strain curves at different temperatures.
We note that as the temperatures to which the components are subjected grow, it is instead preferable to choose PA66.
For the medical sector, which represents another important reference market for polyamide-based polymers, in applications in contact with hot water or drinking water, PA66 GF is the favorite material.