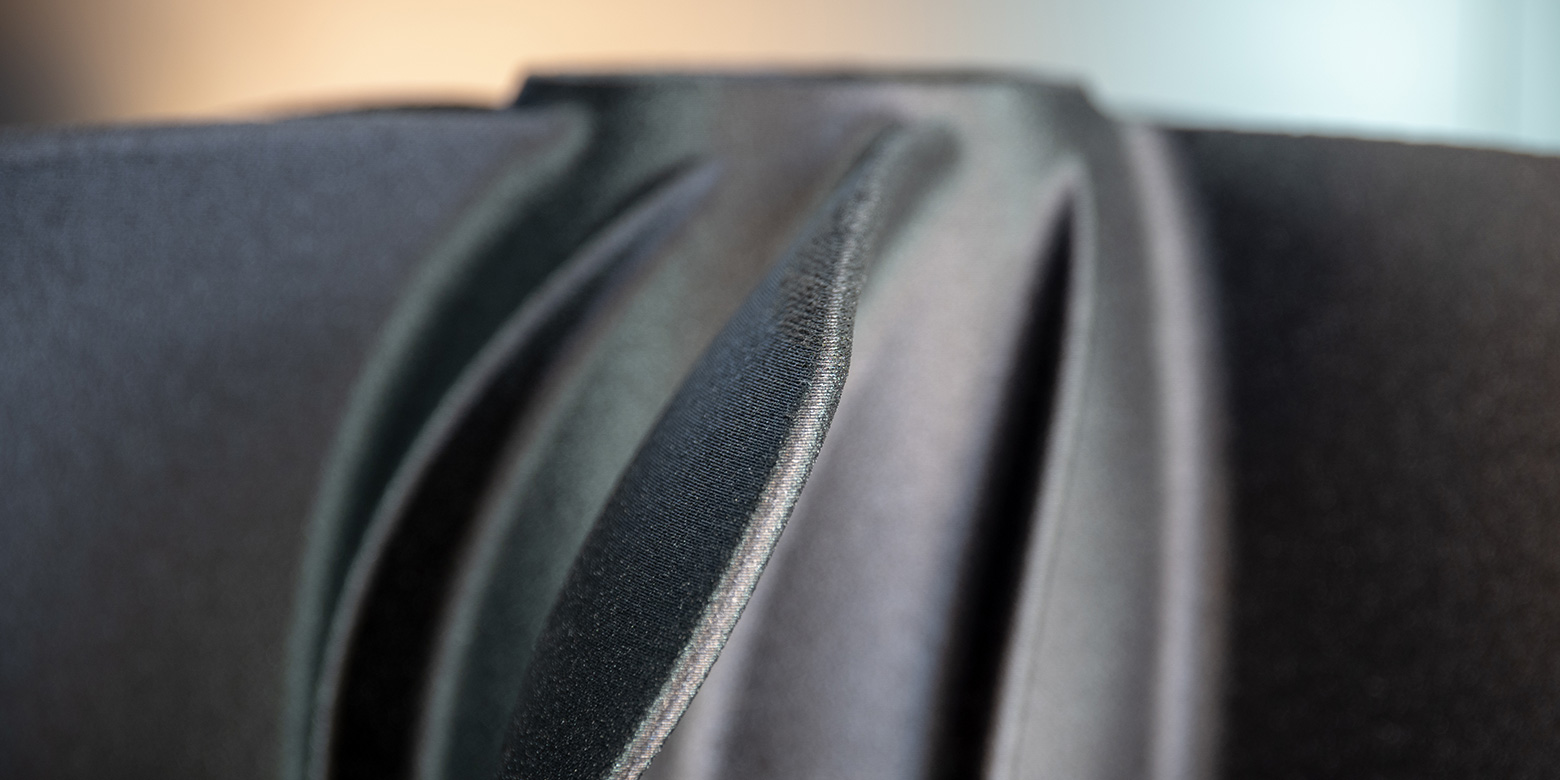
Materiali compositi per l'Additive Manufacturing
Un materiale composito è una combinazione di due o più materiali semplici, al fine di sfruttare le qualità dei costituenti e di migliorarne le caratteristiche meccaniche.
Si combinano fibre e matrice: la MATRICE funge da legante e da supporto (negli sforzi di compressione) e le FIBRE agiscono da rinforzo (negli sforzi di trazione).
Si riscontrano numerosi vantaggi e risultano migliorate le seguenti proprietà:
- Resistenza meccanica;
- Rigidezza;
- Peso (minore del 25%);
- Resistenza alla corrosione;
- Resistenza alle sollecitazioni dinamiche (urti e fatica);
- Smorzamento interno del materiale;
- Isolamento acustico;
- Resistenza all’aggressione chimica e inattaccabilità da muffe e microorganismi;
- Capacità di assorbimento dell’energia di crash;
- Ripartizione delle sollecitazioni su un numero elevatissimo di fibre;
- Possibilità di ottenere materiali con caratteristiche di conducibilità termica ed elettrica adeguate alle esigenze;
A fronte di questi vantaggi, però, i compositi presentano anche degli svantaggi che si possono riassumere nel modo seguente:
- Elevato costo rispetto alle leghe metalliche leggere (circa 3 volte);
- Difficoltà di riutilizzo e smaltimento dei materiali;
- Riparazione dei manufatti spesso del tutto inefficace (irreversibilità dei danni);
- Difficoltà nel controllo e nell’analisi dell’integrità dei materiali;
- Minore resistenza e durezza della matrice rispetto alle fibre;
- Proprietà trasversali talvolta molto più basse di quelle nella direzione delle fibre (materiale anisotropo);
- Possibile invecchiamento del materiale della matrice.
Fibre
Fibra di carbonio: i materiali compositi fabbricati utilizzando fibre di carbonio come rinforzo di matrici di resine polimeriche come le epossidiche, sono caratterizzati dall’avere una buona combinazione di peso leggero, elevata resistenza meccanica e alta rigidità (modulo di elasticità).
Queste proprietà rendono particolarmente interessante l’utilizzo dei materiali polimerici compositi con fibre di carbonio per applicazioni aerospaziali; sfortunatamente, il costo relativamente elevato rispetto alle fibre di vetro, rende queste ultime più utilizzate grazie anche alla loro versatilità. Sono prodotte per PIROLISI (rottura delle macromolecole e riscaldamento), CARBONIZZAZIONE (consente di ottenere il carbonio elementare; T=1000±1500 °C) e GRAFITIZZAZIONE (consente di ottenere il carbonio in cristalli per aumentare la resistenza e il modulo elastico; T=1800 °C) del RAION, del POLIACRILONITRILE (PAN) o di altri sintetici.
Commercialmente, le fibre prodotte dal RAION sono processate in forma di filato continuo, che consiste in 2 fili ritorti insieme, ciascuno costituito da 720 filamenti. Il diametro nominale del filato è circa 5 μm. Le fibre basate sul PAN sono invece fornite sotto forma di corda non ritorta di circa 10.000 filamenti. Peso leggero, alta rigidezza, ottime caratteristiche meccaniche.
Fibra di vetro (tipo E e tipo S): hanno resistenza a trazione e modulo di elasticità inferiore rispetto alle fibre di carbonio e aramidiche ma densità e capacità di allungamento maggiori.
Il vetro è caratterizzato da un comportamento a sé che non è di tipo solido: nel tempo si ha uno scorrimento delle fibre.
Matrici
Resine termoplastiche: materiale polimerico che rammollisce se portato a temperature prossime a quella di fusione, e indurisce se portato a temperatura ambiente.
- Polietereterchetone (PEEK)
- Polieterchetone (PEK)
- Polieterimmide (PEI)
- Polipropilene (PP)
- Poliammide (PA)
Resistenza a trazione
Nel diagramma stress-strain è racchiuso il legame costitutivo della fibra e della matrice, ma anche la capacità delle fibre di resistere agli sforzi nettamente più alti a quelli applicati alla sola matrice, e la capacità di deformarsi della matrice. Durante una prova di trazione, all’inizio le fibre e la matrice si trovano nel campo elastico, dopodiché le fibre continuano a deformarsi ma la matrice si troverà in campo plastico. Quindi riassumendo, quello che può accadere è:
- Deformazione Elastica F+M;
- Le fibre si deformano elasticamente ma la matrice è in condizioni plastiche (anche se accade che le F si rompano prima che M plasticizzi);
- F+M deformate plasticamente;
- Le fibre si fratturano, si frattura anche il composito.
Resistenza a compressione
Le fibre sono costipate dalla matrice, cioè avremo l’effetto della matrice che ostacola i movimenti delle fibre. In questo caso è difficile parlare di carico critico. Quello che possiamo fare è definire due casi: sottoposto a carico di compressione, la lamina può deformarsi secondo un extension mode o secondo uno shear mode. Nel primo metodo abbiamo che la deformata delle singole fibre, a causa della percentuale delle fibre e del carico che sto applicando o a causa di discontinuità della matrice, le deformate sono in opposizione di fase, quindi, si generano nella matrice sforzi di trazione e di compressione. Nello shear mode le fibre si deformano “in fase” e si generano sforzi di taglio. In questo caso abbiamo il fenomeno di buckling. all’aumentare della % delle fibre la resistenza al buckling cresce più nell’extension che nello shear mode.
Stampa 3D
La stampa 3D si presenta come una soluzione ai molteplici problemi, sia di natura ingegneristica sia di natura ambientale. I compositi rinforzati con fibre di carbonio e di vetro sono largamente impiegati nelle tecnologie di stampa 3D.
Ad esempio, la figura successiva mostra dei componenti assimilabili a passacavi, supporti per sensoristica, realizzati in Nylon Carbon Fabbrix®
Il materiale in esame è dotato di buona resistenza al calore e alla rottura. Il nylon conferisce tenacità e resistenza, mentre il carbonio assicura leggerezza e stampabilità.
Le parti stampate sono resistenti e ruvide al tatto, con un effetto leggermente metallizzato. Il materiale necessità di essiccamento in forno per eliminare l’umidità, e questo avviene a 75°C per circa 5-6 ore.
La stampa è avvenuta alle seguenti condizioni:
- T° Estrusione: 260 °C
- Velocità di stampa: 40 mm/s
- Piano: 75°C
I componenti realizzati sono utilizzati principalmente in applicazioni per il settore automotive, dove la continua richiesta di materiali con elevate performance meccaniche colloca il Nylon Carbon in prima linea tra i materiali compositi più lavorati con la stampa 3D.
Contattaci per maggiori informazioni