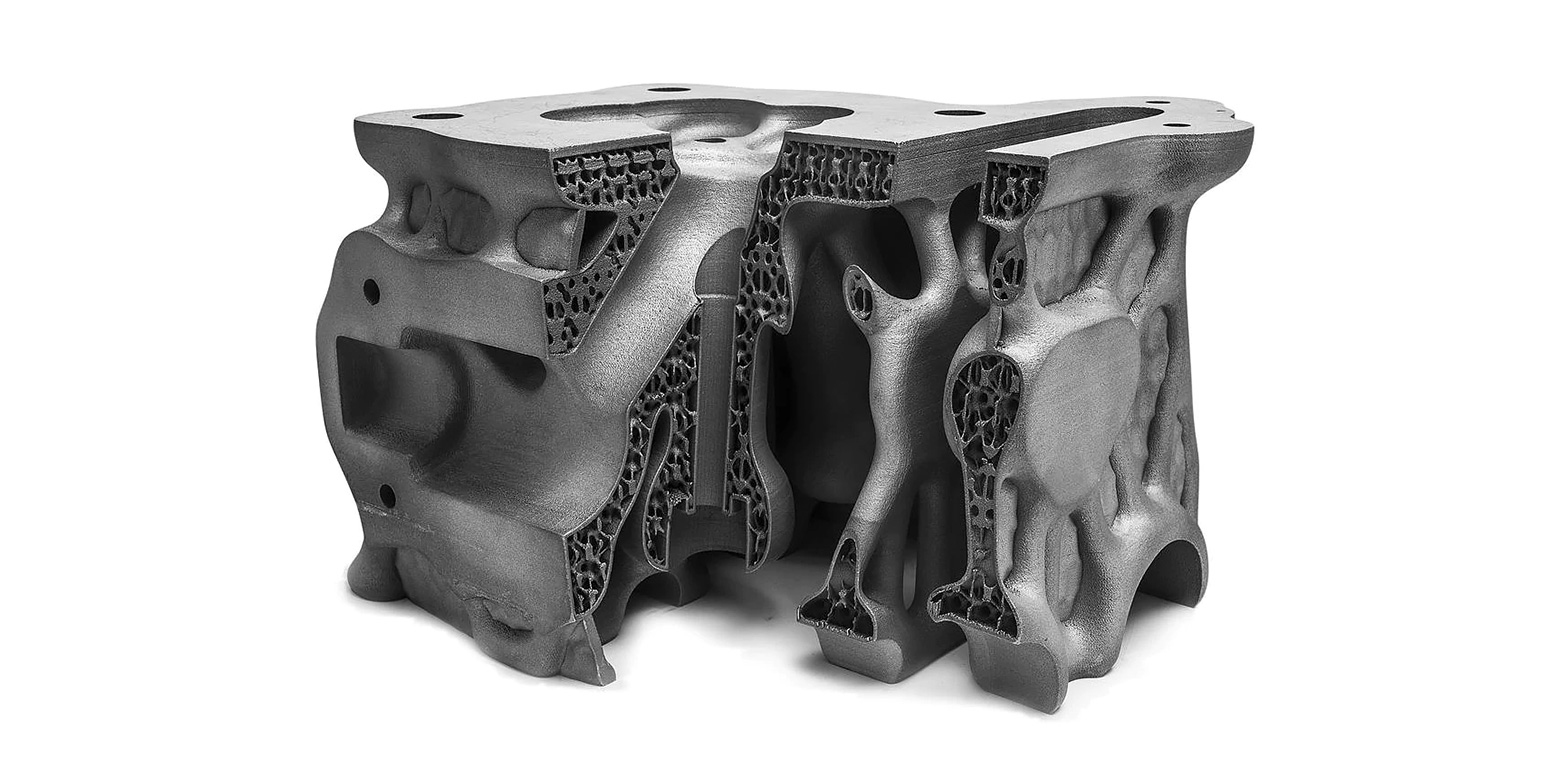
DfAM - Criteri di progettazione per la stampa 3D FFF
La tecnologia di stampa 3D a filamento (FFF) prevede alcuni criteri di design, da seguire per non incorrere in problemi in fase di stampa. Discutiamo nel dettaglio alcune delle regole del DfAM (Design for Additive Manufacturing).
SMUSSI E RACCORDI
Il primo criterio riguarda gli spigoli del componente, in quanto si consiglia di smussare uno spigolo a 45° o raccordarlo. In figura viene mostrato questo piccolo ma fondamentale accorgimento per evitare il fenomeno di warping, ovvero una deformazione anomala con relativo sollevamento dal piano di stampa che, se si verifica si dall’inizio, comprometterebbe la parte per tutto il restante tempo di stampa.
ADESIONE AL PIANO
L’adesione al piano è uno dei grattacapi di chi utilizza tecnologie in ambito AM, ed è influenzata da molteplici parametri come:
- Temperatura del Piano di Stampa
- Percentuale di sovraestrusione del Line Width (consigliabile un 20%)
- Altezza del layer iniziale
- Utilizzo di Brim o Raft
- Velocità di stampa del primo layer (deve essere <35mm/s)
- Ventola di raffreddamento (se si raffredda un materiale che non ha bisogno si ottengono ritiri volumetrici o distacco dal piano)
- Spessore del bottom
- Percentuale di riempimento (non deve essere troppo elevata)
Inoltre, è molto importante progettare il componente in modo da distribuire al meglio il carico sul piano di stampa. In figura ne è illustrato un esempio.
PRECISIONE
Una buona precisione di stampa dipende maggiormente dal diametro dell’ugello che si sta utilizzando. Se lo spessore della linea è minore del diametro ugello ci saranno dei vuoti sul componente (come in figura). Il limite massimo della passata deve essere non inferiore al 70% del diametro dell’ugello.
- un diametro dell’ugello più piccolo comporta una stampa con dettagli elevati
- un diametro più grande contribuisce a ridurre i tempi di stampa
- un ugello con diametro da 0.4 mm costituisce un vero e proprio compromesso, e infatti è il più utilizzato
RESISTENZA DEL COMPONENTE
La tecnologia FFF è anisotropa, ovvero le caratteristiche del componente sono diverse e indipendenti tra di loro lungo le tre direzioni, e tutti i materiali anisotropi non necessitano di raffreddamento. Molte volte si progetta un componente con la consapevolezza di doverlo realizzare con la stampa 3D a filamento, e per questo bisogna tenere conto di come il componente deve essere posizionato sul piano di stampa. Pertanto, è necessario analizzare in anticipo le forze agenti per valutare il corretto orientamento della parte, o per lo meno valutare i requisiti funzionali che il componente deve possedere (funzioni estetiche, resistenza, etc).
Se si vuole dare importanza all’estetica, si dovrà posizionarlo come a sinistra, a discapito di una minore resistenza meccanica e di un aumento della velocità di stampa. Se invece si vuole beneficiare di una buona resistenza meccanica, si dovrà posizionare il componente come nella figura di destra, a parità di velocità di stampa e di qualità estetica. Se non è importante la qualità estetica ma si vuole un tempo di stampa ridotto bisognerà posizionare il componente come nella figura centrale, che evidenzia un compromesso tra le due precedenti.
ANGOLI DI SBALZO
Un ultimo criterio riguarda la progettazione di parti a sbalzo, in particolare di quelle geometrie che presentano angoli formati con il piano di stampa. Come si nota dalla figura, con un angolo minore di 45° è necessario utilizzare i supporti, altrimenti il componente potrebbe cedere in fase di stampa in quanto i layer in quella zona non trovano un punto d’appoggio.
I criteri appena illustrati permettono una buona riuscita della stampa della parte ed eventualmente consentono di apportare modifiche e di revisionare il componente in fase di progettazione a seconda delle esigenze desiderate. Se si vuole sviluppare un nuovo progetto o revisionare uno già esistente, è opportuno intervenire nella fase di design e quindi precedente alla stampa.
BRIDGING
Il bridging in FFF si verifica quando la stampante deve stampare tra due supporti o punti di ancoraggio. Poiché non c'è nulla su cui costruire, non viene offerto alcun supporto per lo strato iniziale da stampare e il materiale tende ad incurvarsi. I ponti si verificano più spesso in fori ad asse orizzontale trovati nelle pareti di oggetti o nello strato superiore (o tetto) di parti cave. Una soluzione è ridurre la distanza del ponte, ma l'impatto di ciò dipende dai vincoli di progettazione della parte. Un'altra soluzione per evitare cedimenti è includere il supporto. Il supporto offre una piattaforma temporanea su cui costruire lo strato “ponte”. Il materiale di supporto viene rimosso una volta completata la stampa, anche se può lasciare segni o danneggiare la superficie dove il supporto era collegato alla parte finale.
FORI VERTICALI
La tecnologia di stampa FFF realizza spesso fori sottodimensionati sull'asse verticale. Il processo di stampa per un tale foro e il motivo per cui il suo diametro viene ridotto possono essere riassunti come segue:
quando l'ugello stampa il perimetro di un foro dell'asse verticale, comprime lo strato appena stampato sugli strati di costruzione esistenti per migliorare l'adesione. La forza di compressione dell'ugello deforma la forma dello strato rotondo estruso da un cerchio in una forma più ampia e piatta (vedi immagine sotto). Ciò aumenta l'area di contatto con lo strato precedentemente stampato, migliorando l'adesione ma allargando il segmento estruso. Questo provoca una diminuzione del diametro del foro da stampare, che può rappresentare un problema quando si stampano fori di piccolo diametro, per cui l'effetto è maggiore a causa del rapporto tra il diametro del foro e il diametro dell'ugello.
Concludendo, la fase di progettazione è molto importante perché permette di intervenire creando un nuovo progetto o revisionando uno già esistente in funzione di come deve essere realizzato. Quindi, conoscendo queste regole si è in grado di agire prima della stampa progettando con dei criteri diversi da quelli applicabili a tecnologie convenzionali, con la possibilità di avere diverse soluzioni in fase di progettazione.